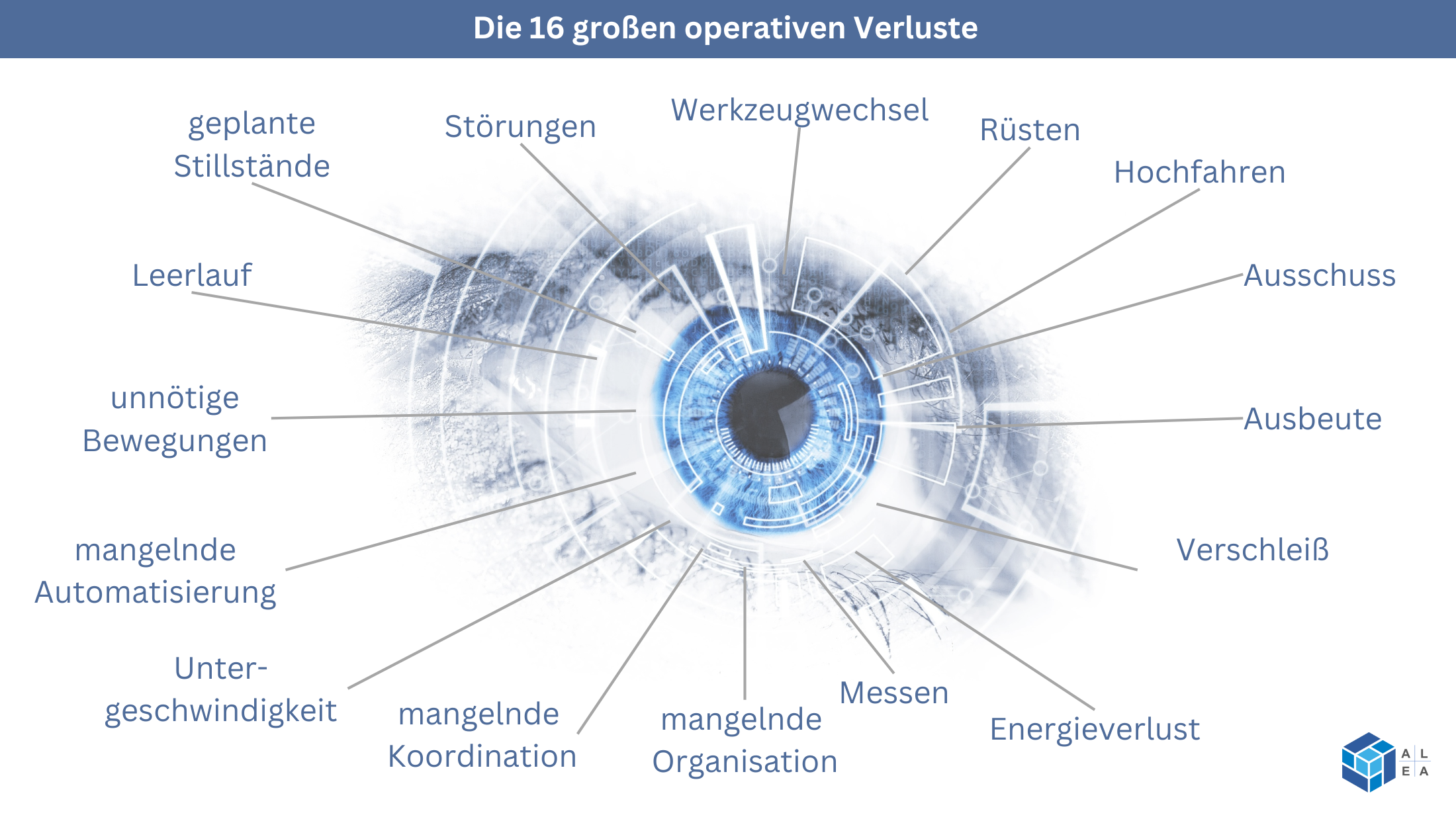
Wettbewerbsfähiger durch kollektives Verbessern - so gelingt Effizienzsteigerung im Alltag
Wahre Effizienz entsteht aus dem kombinierten Denken und Handeln aller Mitarbeitenden – zum Besseren.
Kosten auf "Kosten der Belegschaft" zu optimieren führt in Zeiten des Fachkräftemangels schneller denn je in die Effizienz-Falle. Der Blick auf "Verluste" im Produktionssystem und die konsequente Reduktion der "16 Verlustarten" beitet eine Alternative zu Cost-Cutting für das Operations-Management. Und sie lenkt die Aufmerksamkeit weg vom Headcount hin zum Produktionssystem.
Einleitung
Kostendenken auf Kosten der Belegschaft führt gerade in Zeiten des Fachkräftemangels schneller denn je in die Produktivitäts-Sackgasse. Wahre Effizienz entsteht aus dem kombinierten Denken und Handeln aller Mitarbeitenden – zum Besseren.
Der Weg zur Wettbewerbsfähigkeit
Um unter den heutigen Rahmenbedingungen wettbewerbsfähig zu bleiben, muss das Produktionssystem bis ans Limit des Möglichen geführt werden. Dies erfordert nicht nur technisches Know-how, sondern auch ein starkes Engagement und tiefes Problemlösungsverständnis bei den Beteiligten.
Verständnis über Verluste
Verluste im Produktionssystem zu erkennen und zu eliminieren ist ein grundlegender Schritt, um Effizienz zu maximieren. Sie dienen als Alternative zum reinen Kostendenken. Diese "16 großen Verluste" geben Orientierung für die Verbesserungsarbeit an der Anlage: Verluste durch...
- Störungen
- Rüsten/justieren
- Werkzeugwechsel
- An-/Herunterfahren der Anlage
- Kurzzeitstörungen
- Untergeschwindigkeit
- Ausschuss/Nacharbeit
- geplante Stillstände
- Unnötige Bewegungen
- Unzulänglichkeiten der Führung
- Hürden in der Organisation
- Mangelnde Automatisierung
- Messen und justieren
- Mangelnde Ausbeute
- Überhöhter Energieverbrauch
- Werkzeugverschleiß
Mitarbeiter befähigen
Mitarbeiter müssen befähigt werden, aus Denken Handeln werden zu lassen. Hier sind einige Schlüsselstrategien:
- Schulung und Weiterbildung: Regelmäßige Trainingsprogramme, um das Verständnis für operative Exzellenz zu vertiefen.
- Empowerment: Mitarbeiter sollten in Entscheidungsprozesse eingebunden werden und die Möglichkeit haben, Verbesserungsvorschläge einzubringen.
- Kultur der kontinuierlichen Verbesserung: Schaffe eine Unternehmenskultur, die kontinuierliches Lernen und Anpassung fördert.
Fazit
Bei allen Management-Fehlern der Vergangenheit, maximale Effizienz bleibt ein erstrebenswerter Zielzustand, ob physikalisch an der Anlage oder im betriebswirtschaftlichen Kennzahlensystem.
Das Maximieren der Effizienz sollte jedoch niemals auf Kosten der Belegschaft gehen und aus reiner Kostenorientierung erfolgen. Stattdessen sollten alle Mitarbeiter ermutigt und befähigt werden, durch ein tiefes Verständnis von Verlusten und effizienzsteigernden Maßnahmen ihre Beiträge zur Gesamteffizienz zu steigern.
Weitere Inhalte
Kennst Du schon LeanGames?
-
Lerne spielerisch alles über Lean Management
-
Brett- und Kartenspiele für Anfänger und Fortgeschrittene
-
Video-Antworten mit weiterführenden Links

5S ZahlenGame
Das 5S ZahlenGame kannst Du einzeln oder gemeinsam mit beliebig vielen Kollegen und Kolleginnen spielen, wobei insgesamt über vier Runden gespielt wird. Du möchtest tiefer in das Thema …
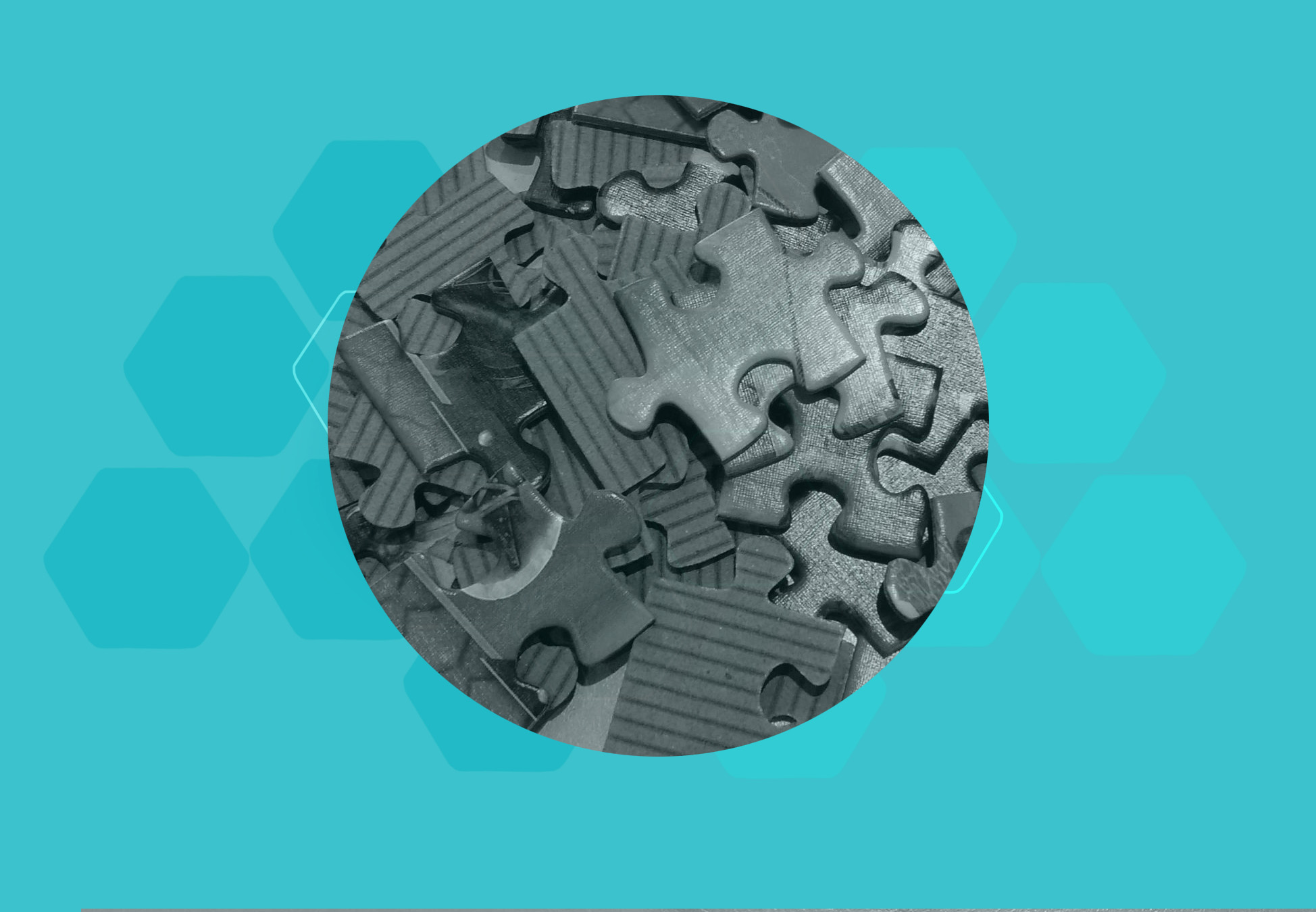
KataGame
Das KataGame orientiert sich an den Forschungsarbeiten von Mike Rother und basiert auf dessen Erkenntnissen, niedergeschrieben in „Die KATA des Weltmarkführers – Toyotas Erfolgsmethode“.
Weitere Inhalte auf LeanNetwork
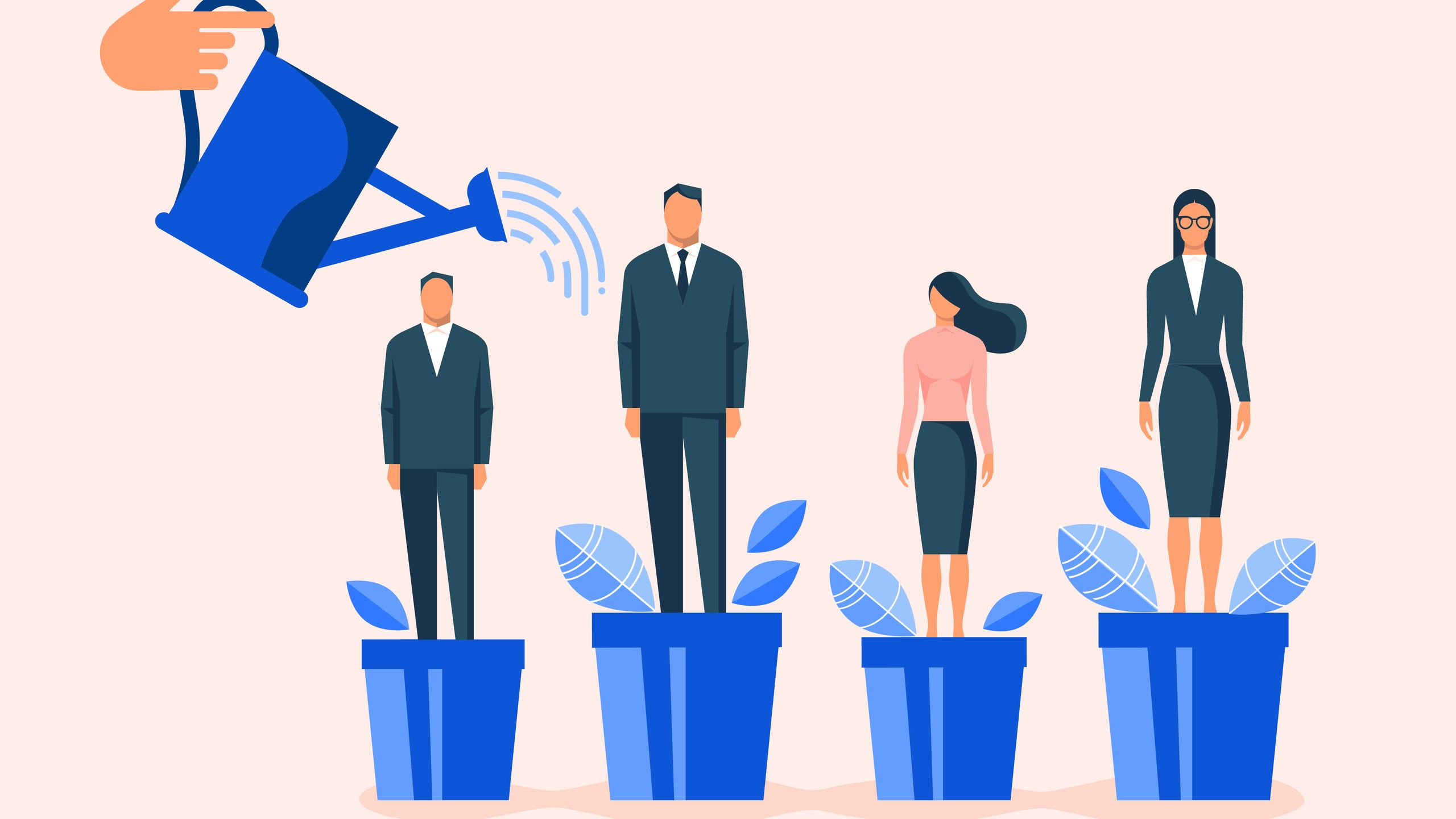
Motivation der Mitarbeiter
Wenn die Entscheidung zur Einführung von Lean Management gefallen ist, sollen möglichst alle begeistert mitziehen. Leider ist das ein ziemlich frommer Wunsch der verantwortlichen …
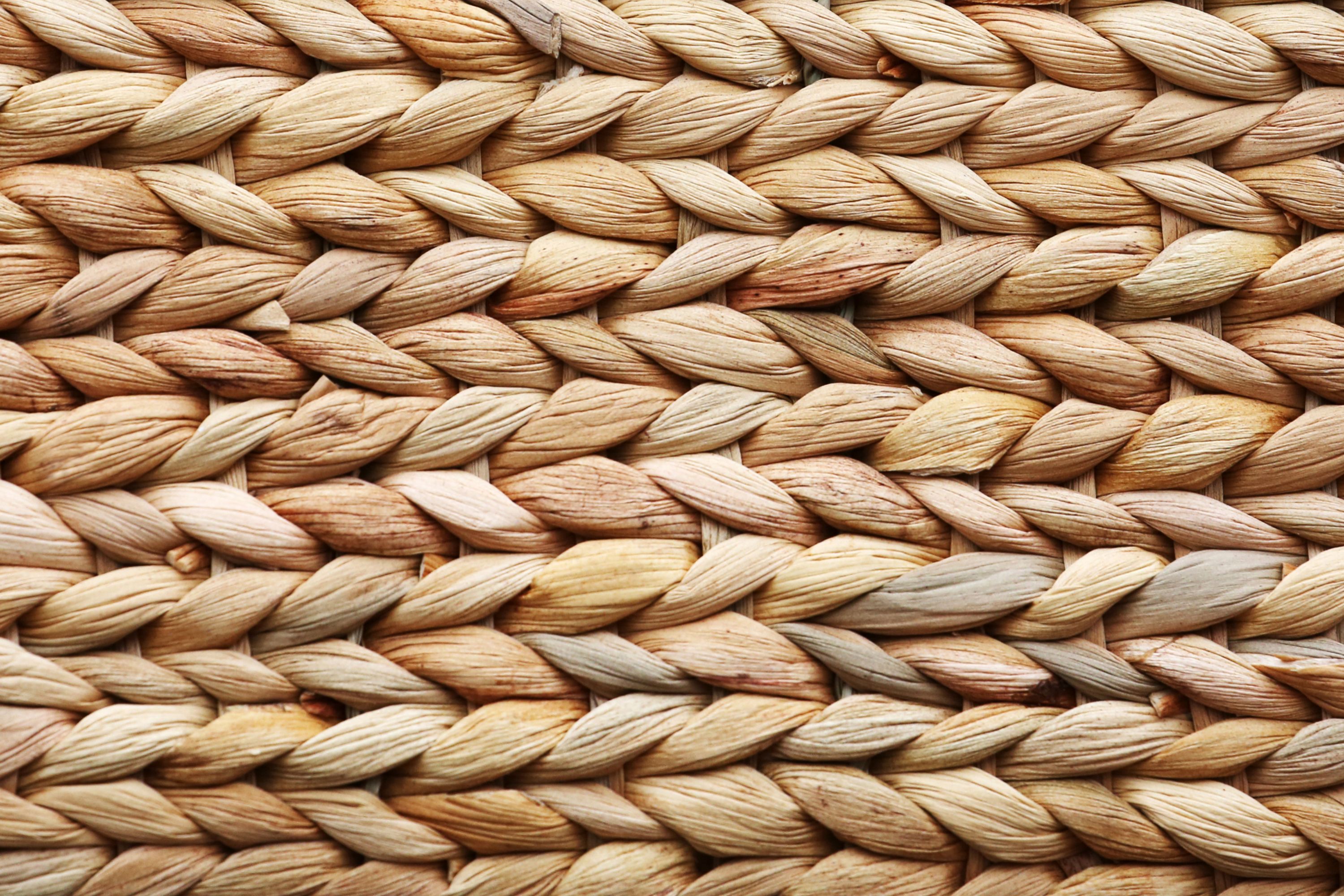
Business Systemics – Unternehmen als Geflecht aus Wertströmen
In Teil 1 und Teil 2 dieser Serie habe ich den Value Proposition Canvas eingeführt und damit 2 der für mich 4 wichtigen Leitprinzipien eines lebensfähigen Unternehmens angerissen, nämlich die …

Lean, Kaizen, KVP: Gefangen in der Methodenfalle
Das Denken und Handeln von gestern und heute ist mit den Herausforderungen von Morgen in weiten Teilen nicht kompatibel. Bei den Themen Lean, Kaizen und Co. ist diese Tatsache besonders …

Warum rein auf Effizienz ausgerichtete Unternehmen keine Zukunft haben
“Warum machen wir eigentlich Lean?” Allein die Frage ist ein möglicher Hinweis darauf, dass die betreffende Person, die diese Frage stellt, nicht hinreichend erfasst hat, was Lean eigentlich …
Kommentare
Kommentar schreiben
Melde Dich an, um einen Kommentar zu hinterlassen.
Teilen